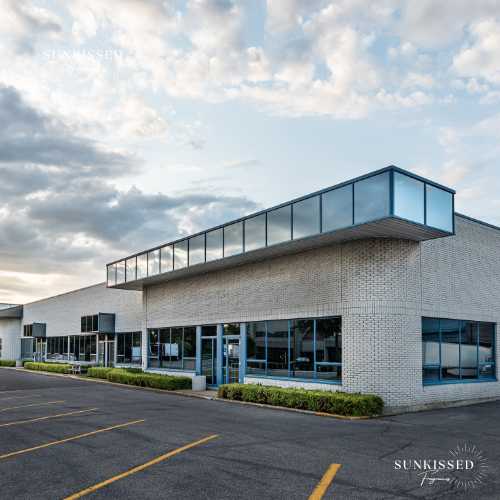
When to Move Your Operations to a Warehouse: Planning for Growth
Deciding to move your business operations from a smaller space, whether it's a home-based setup or a small office, to a warehouse is a significant step that requires careful consideration and planning. This blog will guide you through the process of determining when it's the right time to make this move, how to assess the increased overhead costs, and how to effectively plan for the transition.
Signs it's Time to Move to a Warehouse
1. Space Constraints
- Inventory: If your current space no longer accommodates your inventory needs, causing overcrowding and inefficiencies in storage and operations.
- Equipment: If you require specialized equipment or machinery that requires more space than your current setup allows.
- Workspace: If employees are cramped or if your workspace can no longer facilitate efficient workflow and productivity.
2. Business Growth
- Increased Demand: If your sales are consistently increasing and you're struggling to fulfill orders from your current space.
- New Markets: If you're expanding into new markets or offering new products that require more storage and operational capacity.
3. Customer Expectations
- Timely Fulfillment: If meeting customer expectations for timely order fulfillment and delivery is becoming a challenge due to space limitations.
- Service Quality: If moving to a warehouse allows you to improve service quality, such as faster shipping times or better inventory management.
4. Cost Considerations
- Financial Feasibility: If your business can afford the increased overhead costs associated with leasing or owning warehouse space.
- Profitability: If moving to a warehouse improves efficiency and allows for economies of scale that contribute to overall profitability.
Assessing Increased Overhead Costs
1. Rent or Mortgage
- Average Costs: Warehouse rental costs vary widely based on location, size, and amenities. In urban areas, expect to pay $4 to $10 per square foot annually, whereas in suburban or rural areas, costs may range from $2 to $6 per square foot annually.
- Budgeting: Include additional costs such as utilities, property taxes, and maintenance in your budgeting.
2. Utilities and Maintenance
- Estimation: Utilities for a warehouse can range from $0.50 to $1.50 per square foot monthly, depending on energy efficiency and local rates.
- Maintenance: Plan for maintenance costs, which can vary widely based on the age and condition of the facility.
3. Equipment and Infrastructure
- Initial Investment: The cost of warehouse equipment (shelving, forklifts, etc.) can range from a few thousand to tens of thousands of dollars, depending on your needs.
- Long-Term Savings: Consider investments that may lead to long-term savings or efficiencies, such as energy-efficient lighting or automated systems.
4. Staffing and Training
- Labor Costs: Factor in additional staffing needs for warehouse operations, with average salaries for warehouse workers ranging from $12 to $20 per hour, depending on location and experience.
- Training Costs: Budget for training programs to ensure staff are equipped to operate efficiently in the new environment.
Planning for the Transition
1. Financial Planning
- Budgeting: Develop a detailed budget that includes all anticipated costs associated with the move and ongoing warehouse operations.
- Financial Projections: Prepare financial projections to assess the impact of increased overhead costs on your business's profitability and cash flow.
2. Operational Planning
- Workflow Analysis: Conduct a thorough analysis of your current workflow and identify areas where moving to a warehouse can streamline operations.
- Logistics: Plan logistics for the move, including inventory transfer, equipment installation, and setting up new operational processes.
3. Legal and Regulatory Considerations
- Permits and Licenses: Ensure compliance with local zoning laws, permits for operating a warehouse, and any environmental regulations.
- Contracts: Review lease or purchase agreements carefully and seek legal advice if necessary to understand terms and obligations.
4. Marketing and Customer Communication
- Communication Strategy: Develop a communication strategy to inform customers and stakeholders about the move and any potential impacts on service or delivery times.
- Market Expansion: Use the move as an opportunity to market your business's growth and improved capabilities.
Determining Square Footage Needs
Calculating the right amount of space for your warehouse is crucial to optimize efficiency and minimize costs. Consider the following factors:
- Inventory Requirements: Estimate how much space you currently use for inventory and project future needs based on business growth.
- Operational Layout: Plan for storage areas, packing stations, and any specialized equipment or machinery.
- Office Space: Include space for administrative offices, break rooms, and meeting areas if needed.
- Expansion Potential: Factor in room for future expansion to accommodate continued growth.
Conclusion
Moving your operations from a smaller space to a warehouse is a strategic decision that can support business growth and operational efficiency. By carefully assessing the signs it's time to move, understanding the increased overhead costs, determining square footage needs, and planning for the transition effectively, you can make a smooth and successful transition to a warehouse environment.
We'd love to hear your thoughts! Have you considered moving your operations to a warehouse? What factors are influencing your decision? Share your experiences in the comments below.